Today let’s talk about daily habits. No, not about you, because I know you are perfect in every way.
Just kidding. You are included too. Actually, you have to be, as you may allow the things I will write about below to happen.
As you read this article, mentally note the parallels or differences that my examples relate to the reality in your company. Hopefully, you’ll find more differences than similarities.
What Is A Habit?
To begin, let’s decode what a daily habit is, so there is a foundational agreement on what we are talking about here. The dictionary defines a habit as a:
- Settled tendency or usual manner of behavior.
- An acquired mode of behavior that has become nearly or completely involuntary.
- A behavior pattern acquired by frequent repetition or physiologic exposure that shows itself in regularity or increased performance facility.
Basically, a habit is normal stuff that people do every day. And by people, I mean the folks that work at your shop. They are good people. Great even. Yet, it is incredibly easy to slip into counter-productive habit behavior that has an adverse effect on your company.
Let’s take a look at one thing common in all shops. How the action starts every day. What sneaky habits could adversely affect the business?
Beginnings
Every day has a beginning. Consider your last work day or even the next one. In your shop, how do they usually start?
Is everyone on time? Does everyone know exactly what to work on and can instantly get started? Has the production floor been staged the day before with the jobs to run today? In every department, do the employees know what a priority is without being told?
Let’s say the start time is 7:00 am. When will the first completed garment hit the table for an order? 7:15 am or closer to 8:00 am? Do yourself a favor and come in early one day. Get there before everyone shows up. Start a pretend project in the back, not so you can work, but so you can observe people filing in and starting their day.
Who comes in first? Observe how they begin their day in their area. This is probably your go-getter and number-one producer.
Who drags in last? Do their daily work habits coincide with their tardiness?
What do you think the annual impact is on your production totals with the morning work habits of your staff?
Here’s A Habit Example
For the sake of argument, let’s say a shop can produce an average of 400 units per hour on an automatic screen printing press. They start at 7:00 am, but they don’t get the first shirt printed until 7:30 am usually. That 30-minute window is what we are looking at here.
Because that equals about 200 shirts that could be produced.
Multiply that by three presses. That’s 600 impressions that were not printed until later on in the day. Annualize that by multiplying by 260 (average number of work days for 2023) = 156,000.
Ouch.
It Gets Worse
Sorry to tell you this, but it gets worse. Mainly because the shop has a mid-morning break, an afternoon break, and also a lunch. Let’s say for discussion that these are at 10:00 am, 12:00 pm, and 2:00 pm, respectively.
There is a problem called the “pre-break break” or the “pre-lunch break.” This is where staff heads to the bathroom, breakroom, or other location to “beat the crowd.” They don’t want to wait and want to get a jump on the bathroom stall or the microwave to heat up that burrito. It is usually five or ten minutes early but can be more.
And, to put a cherry on it, that same delay happens after the breaks or lunch getting back to work. Everything is extended by five or ten minutes.
It doesn’t seem like much, and your managers haven’t ever said anything about it to anyone. Some of them are just as guilty.
For the sake of discussion, let’s say it is five minutes early and five minutes after per break period. With two breaks and one lunch per day, that adds another thirty minutes daily that the three automatic screen print press team isn’t fully working.
Yep, when annualized, another 156,000 impressions could have been printed with that time. (for a total of 312,000 for the year)
Other Habits Around the Shop
It isn’t just production, either.
How often have you had a loading dock full of inventory from UPS or FedEx and waited until tomorrow or the next day to receive them into the system?
Are you waiting for the digitization of embroidery orders or screens to be burned on the same day you run those orders?
Take a look at the cadence of how garments are ordered; art is created or separated, or even when customer information starts the order entry process.
How often is one department waiting on another to complete something so they can start their work? By the way, one of the most common wastes to eliminate if you are on a lean manufacturing journey is “waiting.”
A Sense of Urgency
What we are really talking about here is a sense of urgency. Have you ever noticed managers walking twice as fast as hourly employees? One person is on a mission to complete something; the other is on the clock and waiting until the shift ends. There could be quite a difference in how they view their roles in how tasks are completed daily.
Of course, bad habits aren’t present in all employees or shops. That said, you have to take stock of what happens daily. People merge into patterns of behavior. These patterns can be positive or negative.
Observing the habits is where you start. Take an assessment with a cold, critical eye. Include your own daily habits in that assessment too.
Notice anything that can be improved? Aspiration starts with dissatisfaction.
Maybe it is time to replace some bad habits with some good ones.
“We are what we repeatedly do. Excellence, then, is not an act but a habit.” – Will Durant
“Chains of habit are too light to be felt until they are too heavy to be broken.” – Warren Buffett
“The difference between an amateur and a professional is in their habits. An amateur has amateur habits. A professional has professional habits. We can never free ourselves from habit. But we can replace bad habits with good ones.” – Steven Pressfield.
Help Support This Blog
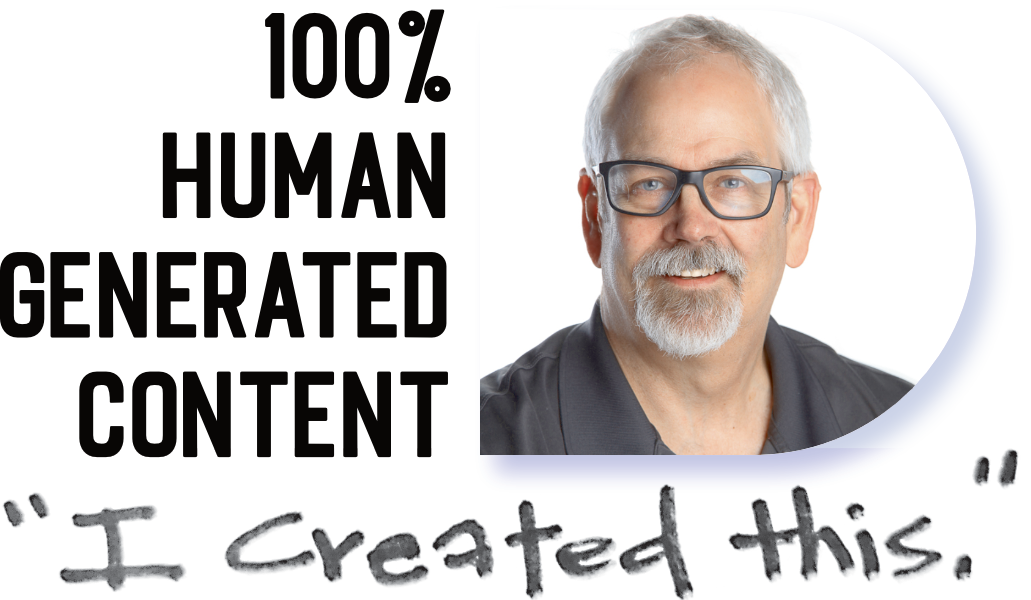
While I may be goofing around with AI for some projects, this blog and its contents have been created by me, Marshall Atkinson.
Why am I writing this? To remind you, dear reader, these words are backed by a real person. With experience, flaws, successes, and failures… That’s where growth and learning happen. By putting in the work.
If you are reading this and it is not on my website, it has been stolen without my permission by some autobot. Please report this to me and/or publicly out the website that hijacked it. And if you are trying to copy and use it without my permission, you are stealing. Didn’t your mama teach you better?
If you like this blog and would like to support it, you can:
- Buy a book.
- Share this blog on your social media.
- Join Shirt Lab Tribe.
- Subscribe to the Success Stories podcast.
- Watch and like an episode on the Jerzees Adventures in Apparel Decorating YouTube series.
- Get signed up for the new Production Tracker app.
Also, my basic elevator pitch to you is that I help with “Clarifying effective change.” If you are dissatisfied with your business’s current results, maybe I can help.
Please schedule a discovery call here if you want to learn more.
Thanks!
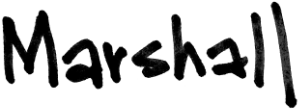
Marshall Atkinson also shares exclusive blog content at Supacolor.com. Supacolor makes The World’s Best Heat Transfer and provides tips, inspiration, and other resources designed to empower professional garment printers.