Do you have an Employee Performance Level Program? This works in concert with your Employee Review Program. You have one of those too, right? One of my coaching clients, Ken, asked me recently if I have written about this previously. Looks like I haven’t. So, Ken, this one is for you.
As your shop grows, it becomes imperative to maintain a high level of employee engagement and productivity. One way to achieve this is by implementing an employee compensation program based on employees’ performance, training, attitude, skill level, communication, and willingness to learn.
In this blog, I’ll show you how to build out a compensation program for employees. We will also use a newly hired screenprinter named Fred as an example. However, the ideas here could work for any position in your shop.
You simply need to detail the expectations for the employee to get to the next level.
At each level, a pay range coincides with the employee’s performance, skill, and learning level. Use this idea with how you compensate your crew. For example, for a screenprinter:
- Beginner Level Screenprinter wage range = $15 per hour to $17 per hour
- Intermediate Level Screenprinter wage range = $17 per hour to $20 per hour
- Advanced Level Screenprinter wage range – $20 per hour to $25 per hour
You get the idea. These dollar amounts may not fit your shop. You set the scale. Feel free to rename the levels “Screenprinter 1” or “Level One Printer” or any other way you want to identify the position.
Again, I’m using a screenprinter as an example, but this could work for any job in your company.
Beginner Level Screenprinter
The Beginner Level is the entry-level position for all employees. At this level, the primary objective is to learn the basic skills required for the job. Employees at this level are expected to have sound soft skills as an employee, including:
- Complete training programs related to their job.
- Demonstrate a positive attitude toward work.
- Meet the minimum performance standards for the beginner level. (This is written out below)
- Communicate effectively with their team members.
- Show a willingness to learn and improve their skills.
- Be punctual.
- Treat coworkers with respect and as professionals.
- Ask questions, even if the material was just taught to them yesterday. (No such thing as a stupid question when you are learning.
These basic skills carry over to all positions and for every employee.
Key results for the Beginner Level Screenprinter:
- Complete all required training programs within the first 90 days.
- Maintain a positive attitude towards work by receiving at least 3 compliments from customers or team members. “I like the way Fred is helping me out!” This means you must regularly talk about your new employee with their teammates.
- Meet the minimum performance standards by achieving a productivity rate of at least 90% of the work assigned in the time frame established. How are you measuring the work?
- Communicate effectively with their team members by attending all team meetings and contributing at least one idea per meeting. Adopt a “No Wallflowers” mentality. Get group discussions and engagement going.
- Show a willingness to learn and improve their skills by attending at least one training session in their department or other areas. You dictate the frequency. Weekly? Monthly?
- Demonstrate core competency with the material taught. They must prove they can do the basic work at an acceptable speed. Quality should not be sacrificed for speed, though.
For a screenprinter, the basic tasks are below. If you are outlining a program for other positions in your company, you should detail these expectations in that position’s job description.
Beginner Screenprinter Job Responsibilities:
The Beginner Level Screenprinter shall learn to set up and operate an automatic or manual textile screen printing press according to written and/or verbal instructions, established company procedures, safety, and quality guidelines.
They should be capable of solving basic printing problems and adjusting the mechanical operation of the press to keep quality, registration, color, and production speed at an optimum level.
The employee must understand inks and solvents at a beginner level and can easily print basic one to three-color designs.
Job Duties:
- Receives production orders and job assignments from the supervisor. Understands the expectations for the output for the day’s shift.
- Verifies that all jobs, screens, inks, samples, and work order documents for 100% of the work to be completed are staged at the press at the beginning of the day.
- Produces work in the priority order established on the production schedule.
- Can read and understand each job order to verify the quantity to be printed, garment color, ink color selection, color sequence, and any potential challenges with the garment.
- Sets dryer for proper drying or curing. This is important when working between various ink sets and fabric types.
- Obtains production screens and check them for the proper color count, sequence, and quality.
- Understands mesh counts, screen tension, EOM, and the mechanical part of printing with a squeegee and how each item governs the amount of ink deposited.
- Uses verified production screens in the proper color position on the press and properly aligns and positions the screens with the appropriate registration tool, such as Tri-Loc.
- Screen registration should be handled in under ten minutes or less for the beginner level.
- Adds the proper durometer squeegee for the design to the press at the correct angle and pressure. Also, add the floodbar and the correct ink for the same screen.
- Tests the registration of the print design by printing on material scraps or pellons until one version is printed with a complete design.
- Inspect the print for print quality, registration, alignment, and opacity. Matches the print to the art approval form or mock-up to check for correctness.
- If satisfied with the initial strike-off, secures supervisor approval for the production run.
- Prints job maintaining optimum production rate, color opacity, registration, and quality standard within established company and customer guidelines, replacing misprinted or unacceptable garments to obtain customer order quantities.
- Meet the minimum performance standards by achieving a productivity rate of at least 85% of the work assigned in the time frame established. How are you measuring the work?
- Prints with a defect rate of under 3% per location.
- Solves printing problems during the print run.
- Responsible for directing the work of the press assistant and the catcher.
- Completes production records or logs.
- Transitions to the next job on the production schedule quickly.
- Ensures proper cleanliness of the press, workstation, and immediate press area.
Intermediate Level Screenprinter
The Intermediate Level is for employees who have completed the basic training and demonstrated their ability to perform their tasks effectively.
At this level, the primary objective is to improve their skills and take on more responsibilities. Employees at this level are expected to handle all of the responsibilities and expectations of the Beginner level.
For the Intermediate Level, there are a few added responsibilities and expectations:
- Complete cross-training programs in other areas. This could be in the screen room, ink mixing, receiving or shipping, or any other departments. Cycling through training in other departments makes the employee versed in what should be expected from those departments. This should happen before the one-year work anniversary date.
- Be able to print up to the maximum color count for the press.
- Start printing with specialty inks, such as puff, discharge, high-density, etc., at a learning level.
- Be able to print more difficult garments such as bandanas, hoodies, sweatpant legs, and polyester-based or technical fabrics.
- Prints with a defect rate of under 2% per location.
- Maintain a positive attitude towards work by receiving at least 3 compliments from customers or team members. “Fred stayed late and finished that important order!” This means you must regularly talk about your employee with their teammates.
- Meet the minimum performance standards by achieving a productivity rate of at least 90% of the work assigned in the time frame established. How are you measuring the work?
- Communicate effectively with their team members by attending all team meetings and contributing at least one idea per meeting. Adopt a “No Wallflowers” mentality. Get group discussions and engagement going. At least once per quarter, they should lead a meeting.
- Take on additional responsibilities and complete them successfully by managing at least one project or task assigned by the manager per quarter. This is a leadership lesson and test. Can they manage a project on their own?
Advanced Level Screenprinter
The Advanced level is for employees who have demonstrated exceptional skills and have taken on leadership roles within the organization. Of course, they can handle everything the Basic and Intermediate Level Screenprinter is expected to produce. On top of those points, the Advanced Level Screenprinter should:
- Be able to train and mentor new employees in the Standard Operating Procedures for production. They teach the “shop way,” not their way.
- More leadership responsibilities should be added, including some employee management. Start them down the management path by having them lead an overtime shift or on a Saturday. Provide them with leadership and management training.
- Give them added responsibilities, such as being part of the safety or sustainability committees. Use their knowledge, skills, and talent to shape a better future for your shop.
- They should have expert knowledge of print mechanics and output. Problems or challenges can be quickly diagnosed and solved.
- An Advanced Level Screenprinter should be self-sufficient. They can burn a new screen if needed. Mix a new bucket of ink to match a Pantone color. Look up a problem in the system and find the answer. Ideally, you want an ownership mentality for the work being produced.
- They have mastered specialty inks at this level and can confidently print any job your sales team sells.
- Prints with a defect rate of under 1% per location.
- Can set up and register jobs in under five minutes per screen.
- Maintain a positive attitude towards work by receiving at least 10 compliments from customers or team members. “Fred helped me understand the problem and quickly gave me the answer i needed to get the print to look great!” This means you must regularly talk about your employee with their teammates.
- Meet the minimum performance standards by achieving a productivity rate of at least 95% of the work assigned in the time frame established. How are you measuring the work?
- Communicate effectively with their team members by attending all team meetings and contributing at least one idea per meeting. Adopt a “No Wallflowers” mentality. Get group discussions and engagement going. At least twice per quarter, they should lead a meeting.
- Take on additional responsibilities and complete them successfully by managing at least two projects or tasks assigned by the manager per quarter. This includes covering the managerial responsibilities for the production floor.
Using Fred as an Example
Let’s assume that Fred has been hired as a screenprinter in your shop.
Fred is a Beginner Level employee, and his primary objective is to learn the basic skills of a screen printer in the next 90 days. See the written outline above. As a shop manager or owner, you are responsible for setting up the basic learning lessons for Fred to be competent and dependable as a screenprinter. These are planned activities that are on a calendar.
Take the time to schedule each step Fred needs to learn and get it on a day on the calendar. Here’s a quick test. What day will you teach Fred about the importance of screen tension, EOM, and mesh counts? If you don’t know that, you aren’t organized well enough.
Fred’s objectives are:
- Complete all required training lessons within the first 90 days. There should be a checklist and a rating system developed by your shop. This includes all of the lessons with dates on a calendar and a named instructor for each lesson.
- If you think it is worthwhile, consider creating a test that Fred should pass. “Hey Fred, please set this two-color job up in under ten minutes.”
- Fred demonstrates a positive attitude toward work. This should match the expectations that his manager has verbalized to Fred. Fred must demonstrate that he is willing to learn and wants more responsibility. That is what you are looking for in a new employee.
- He should be punctual when Fred shows up for work and with assignments.
Fred’s key results are:
- Complete all required training programs within the first 90 days.
- Demonstrate basic level competency.
- Receive at least 3 compliments from customers or team members.
Once Fred successfully completes all the required training programs within the first 90 days he can move up to begin work on the Intermediate Level.
Your Own Fred
Fred is an example. For your shop, you have your own version. New employees don’t know anything. Your job is to give them the correct expectations and train them on how to accomplish them.
If you don’t say something, they won’t know it. In fact, sometimes you have to verbalize something a dozen times or so before it sinks in. Be patient. What is easy for you is unimaginable for a newbie.
Make it fun. Be prepared. Document the right way and show your own Fred how to do something.
Need help? Reach out!
“What we can control is our performance and execution, and that is what we are going to focus on.” – Bill Belichick
“I can only control my own performance. If I do my best, then I can feel good at the end of the day.” – Michael Phelps
“An ounce of performance is worth pounds of promises.” – Mae West
Help Support This Blog
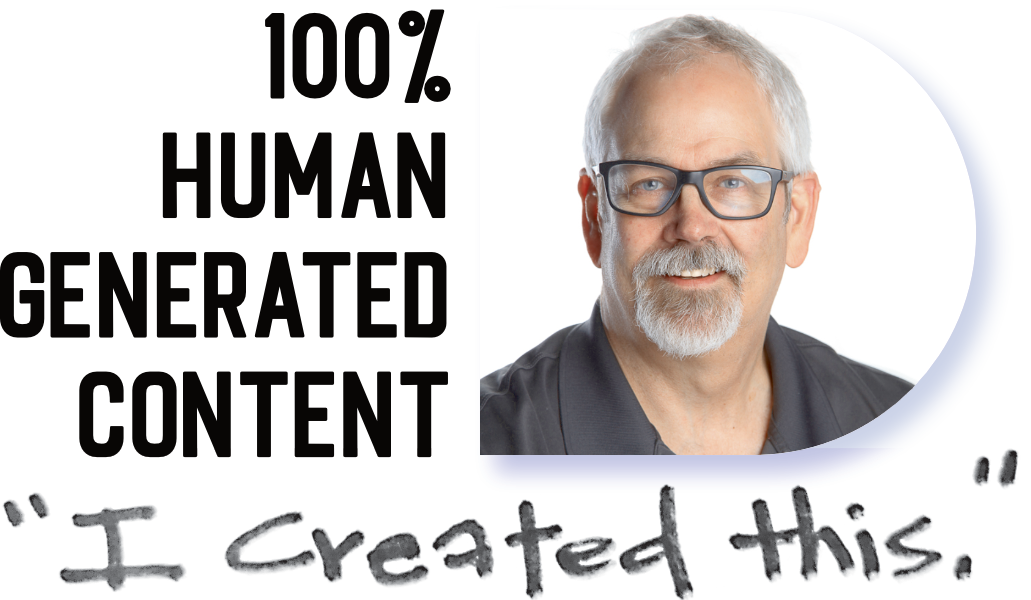
While I may be goofing around with AI for some projects, this blog and its contents have been created by me, Marshall Atkinson.
Why am I writing this? To remind you, dear reader, these words are backed by a real person. With experience, flaws, successes, and failures… That’s where growth and learning happen. By putting in the work.
If you are reading this and it is not on my website, it has been stolen without my permission by some autobot. Please report this to me and/or publicly out the website that hijacked it. And if you are trying to copy and use it without my permission, you are stealing. Didn’t your mama teach you better?
If you like this blog and would like to support it, you can:
- Buy a book.
- Share this blog on your social media.
- Join Shirt Lab Tribe.
- Subscribe to the Success Stories podcast.
- Watch and like an episode on the Jerzees Adventures in Apparel Decorating YouTube series.
- Get signed up for the new Production Tracker app.
Also, my basic elevator pitch to you is that I help with “Clarifying effective change.” If you are dissatisfied with your business’s current results, maybe I can help.
Please schedule a discovery call here if you want to learn more.
Thanks!
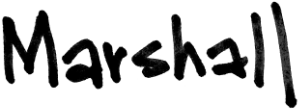