How do you make decisions on what to improve? Sometimes in our lives or work, we get so backed up it is difficult to tell what to work on first. I’ve been there.
Because everything needs improvement, nothing gets improved as there isn’t any action.
You’ve heard about making a “decision tree,” where someone sketches out a diagram with inputs and consequences that, if used, result in an outcome. That’s great, but it isn’t going to help you get caught up if you are in the weeds 87 orders behind in production.
Instead, I want you to focus on just a few things. Let’s keep it simple. But you are going to need to execute rigorously.
How You Use Time
Time is the most valuable commodity you have in your business. How is it being spent?
If I was to come out to your shop and help get you back on track, this is where I would be spending a good chunk of my effort. There are only so many minutes in the day. The daily effectiveness of your team and the level of their performance during their shift matters more than anything.
Only One Person Knows How to do Something
When there is a lot to do, is this person being tasked to be in two places at once? Educate more people and get more work handled simultaneously.
If you are the owner of a small shop, this could be you. Doesn’t it bother you that more people haven’t be properly educated? Imagine how much time you would have a day if you weren’t involved in the daily grind.
You have to make time to solve this problem. Train more people to make decisions so you don’t have to make them.
Waiting
There can’t be any waiting in this industry. Usually, one department is waiting on another to complete a task so they can get to work.
Look upstream and see what you can do to have that task completed at least one business day before someone needs something.
For production, in any department, 100% of the work should be staged and ready at the machines for tomorrow by the end of work today. I call this the “Scavenger Hunt” and it is the responsibility of the department head to ensure that it is handled daily. They don’t have to physically do the work, but the should not leave for the day until it is completed. No excuses.
When your crew has what they need, and a priority list or SOP on what to do next, nobody has to make a decision. It’s all action.
Information
People spend a lot of time asking, “Hey, what’s this mean?” or worse, the information is missing altogether.
It’s hard to receive new inventory that was just dropped off by UPS when there isn’t a PO number or order number on the packing slip to identify that it belongs to order #123456.
Think of the dilemma facing your printer or your embroiderer when the color to use is labeled as “blue” or “tonal.” What are they supposed to do with that?
Look to see how you can tighten up your information trail. Having accurate and complete information allows staff members to execute and make good decisions themselves.
Not Being Ready to Work
What time does your production crew clock in every day?
For example, let’s say that it is 6:30 am. At what time is the first shirt finished in production at each machine? 6:37 am or 7:12 am?
Want to really be upset? Start tracking the lag in the morning, just before or after break, and just before or after lunch. I’ve tracked this in some shops and it is nearly an hour a day. Annualize that.
Let’s just say that you run four automatic screen printing presses and they have thirty minutes of “not being ready to work” time per day. If they average 400 impressions per hour, on an annual basis that could be costing you: 400 (impressions per hour) x .5 (30 minutes daily) x 220 (work days) x 4 (presses) = 176,000 impressions.
Observe what is happening daily on your production floor and do the math.
Not Having Standards and Processes
In your shop, is there a “shop way” of doing every task? From how to answer the phone, to how to tape up a box, every action in your shop should have it’s own method.
When Bill, Maria, and Jose all do the same tasks differently, what is the expected outcome? Don’t take my word for it. Talk to all three staff members and decide which way works the best and make that the standard.
Document it, and start educating other staff members on the method. When there is a right way and a wrong way of doing something, it makes things easier.
What are you tolerating daily in your shop?
Not Working as a Team
How would you rate the teamwork in your shop? Seriously.
I want you to mentally picture your press operator transitioning from one job to the next. Is there a flurry of activity as other people help get the old screens and ink out of the way and the new ones inserted on press? What about the inventory? Is someone catching the shirts as they come down the dryer belt, counting them and boxing them up? They then mark the job complete and start getting the new inventory for the next order ready.
Often, I see one person struggling to do all of that as the other team members slink off to the bathroom, take a smoke break, or get a Coke.
Maybe the real reason why your production crews can’t get more work out a day is that they don’t function as a team.
Sound Print Mechanics
Start thinking about time in production. How long should each step take?
What is the difference between printing 4 shirts a minute and 7 shirts a minute? That’s only 3 shirts right?
Hmm. Here’s the math:
4 shirts per minute x 60 minutes = 240 impressions per hour.
7 shirts per minute x 60 minutes = 420 impressions per hour
Why does this matter? If you are actually printing shirts five hours out of an eight hour shift with an automatic screen printing press, are you getting at least 2,100 impressions daily?
Why not? The list of excuses from your print crew should help you make the decisions on what to fix.
Here’s what that looks like on an annual basis per press, by the way:
240 impressions per hour x 5 hours per day x 220 days per year = 264,000 impressions.
420 impressions per hour x 5 hours per day x 220 days per year = 462,000 impressions.
Same amount of time printing per day, but a 175% difference. All for ramping up 3 shirts per minute faster.
Decisions to Make
The truth is that I’m not at your shop. I don’t know the reasons why you might be struggling. Maybe you aren’t really struggling, but just want to improve.
It all comes down to how you use time effectively. Start asking “why are we doing it this way?” Chances are, nobody knows. There may be a better way.
Take 30-minutes a day to work on how you use time. It will be the best decision you can make in your business.
“The risk of a wrong decision is preferable to the terror of indecision.” – Maimonides
“There is no decision that we can make that does not come with some sort of balance or sacrifice.” – Simom Sinek
“Urgency creates decision making.” – Kevin Brady
Help Support This Blog

If you are reading this and it is not on my website, it has been stolen without my permission. Please report this to me, and/or publicly out the website that hijacked it. And if you are trying to copy and use it without my permission, you are stealing.
If you like this blog and would like to support it, you can:
- Buy a book.
- Share this blog on your social media.
- Join Shirt Lab Tribe.
- Subscribe to the Success Stories podcast.
- Watch and like an episode on the Jerzees Adventures in Apparel Decorating YouTube series.
- Get signed up for the new Production Tracker app.
Also, my basic elevator pitch to you is I’m that help with “Clarifying effective change.” Please schedule a discovery call here if you need help and want to learn more.
Thanks!
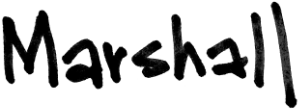
Marshall Atkinson also shares exclusive blog content at Supacolor.com. Supacolor makes The World’s Best Heat Transfer and provides tips, inspiration, and other resources designed to empower professional garment printers.