The time is now to upgrade your Receiving Department Processes.
Why?
For starters, you are not working the same way as you were pre-COVID. We used to get the inventory for any order in one shipment, or maybe occasionally two. These days, it is not uncommon for the goods to be sourced from four or five different warehouses and from multiple garment distributors.
This is causing havoc with Receiving teams as they are constantly counting and adding another batch of shirts to an already partial order. Lately, I’ve been working with shops on their process and workflow in this area.
I thought it might be handy to give some tips to help your Receiving team too.
Remove the Clutter
If there is one thing that we’re really good at in this industry it is keeping stuff “just in case.” You never know when you might need some purple hoodies or a case of navy blue hats with an orange brim. That’s why they are sitting right there in the way.
But the problem with those boxes and other items that you are not immediately using is that it takes time to work around them. You are constantly walking around these challenges.
You need the space for higher priority organizational effort. As most shops are not gigantic, the square footage that you need for jobs on the schedule is being taken by the detritus of “what if?”
Do yourself a favor and clean house. Have a garage sale. Donate to charity. Move it to another location. Whatever it takes. Clear it out so that you have big open areas on the floor and shelving units with nothing in them.
We’re going to need that.
The mandate is that you should be ready to work.
Prioritize the Real Estate
The next thing we want to do is to prioritize the real estate in the Receiving Department. You need big chunks of area for these things:
- Open area to receive from delivery trucks. This is kept empty and ready to work. That beep, beep, beep sound you hear means that it is about to get filled.
- Empty tables that can be used for sorting and counting. Not for storage. These are kept clean. No food or drinks are allowed on them. You know why.
- Easy access to computer workstations. These should be raised up so you can work while standing, and also more like an express lane at the grocery store than a desk situation.
- Area to put Partially Received Orders. Lately, this needs to be about 30%-60% bigger than normal. Find the room.
- Area to put Fully Received Orders. Ideally near the Production Department so they can pick their own orders.
- Area to put UFO Orders. These are the unidentified boxes of goods that have arrived and you don’t or can’t link them up with an order yet as you need more information. For contract decorators, this is a must-have.
- Working lanes that are kept free. Hand-carts, skids with a pallet-jack, and forklifts need to travel easily. Use tape on the floor.
Use a System
There are plenty of shops out there that don’t have a computer system that runs their shop. Instead, they use spreadsheets, clipboards, job jackets that hang on the wall, or whiteboards to control everything.
While the shop may think that they are “saving money” by operating this way, it probably is causing more harm than good. Do yourself a favor and get more information and upgrade to a computer system.
The rest of this article will focus on those that use a system.
A Great Receiving Process Starts With Daily Rules
- Items received must be checked in the day they arrive. There is no waiting. You can not do it tomorrow.
- The area must be kept clean, clutter-free, and ready to receive or process items. Tools are in place and ready to use.
- There should be adequate space reserved for organizing and processing items in the Receiving department. Anything not in use should be removed.
- Items received will be checked in via the packing slip that accompanies the shipment. Check against this first, then process against the information in your system.
- Recognize that the priority is to ascertain that the inbound items should match what was expected or ordered.
- Work smallest to largest for the daily counts. Usually, small quantities are the remaining pieces for an order to make it complete.
- When in doubt, recount.
- Damaged items or packages need to be documented immediately and acted upon. This needs to be communicated to the front office quickly for instructions on what to do. These are placed in a special area and cataloged.
- There are six statuses, “Not Received”, “Partially Received”, “Fully Received”, “Wrong Item”, “Damaged, or “Not in the System.” Everything in the department is counted and falls into one of these categories. All items are processed before being put away.
- Before anyone leaves for the day, the area is staged and prepped for tomorrow’s receiving. Make ready for a new influx of goods to be check-in. Empty skids are ready, tables are cleared, trash cans empty.
Seven Areas for the Receiving Department
- Incoming area to be processed. This is just off the truck. You will be segregating the packages here for processing.
- Counting area. Tables are set up. Supplies furnished. Here’s where you process each package.
- Receiving Workstations. Your computers, printers, filing storage, etc.
- Partially Received Area. This is the space where you keep the inventory while you are waiting for the rest of it to be delivered.
- Fully Received & Staged for Production Area. This stuff is ready to be decorated by your production team.
- Damaged or Error Area. This is your purgatory area while you process the return.
- NIS (Not in System) Area. This area is where you stage items that are challenges that need a resolution, such as when a box shows up that doesn’t match anything in your computer system.
Beginning of the Day – Ready to Work
Each workday begins with the Receiving Department completely ready for the daily intake of new items to process.
The area is clean, neat, and orderly. This is arranged at the end of the previous day.
Prepare a list of what is to arrive today is processed and printed. You should know:
- How many packages should be arriving?
- Are there rush order items or critical packages that are coming in and need to be immediately rushed to someone or a department?
- Any shipments coming in LTL?
- Are customers dropping off items?
- Any scheduled shipments arriving?
Ideally, your Receiving team is in steady communication with your other departments. You want to prepare for tomorrow’s work sometime today if you can.
The best time to prepare for today’s work is before you leave yesterday. This is a good habit to have and should be encouraged.
Receiving Department Freight Delivery Process
UPS, FedEx, USPS, or even an LTL truck backs up and has some packages for you. Great! You should be ready to receive anything they have.
Here are some simple process steps for you to use to start building your own:
- Ask the freight carrier driver how many packages they are dropping off. Do not let them leave or sign anything until you have verified that you have the same number in the building.
- As the items are being unloaded, start segregating them by individual orders. On the shipping label, it will say 1 of 1, or 2 of 5, etc. Have a skid, table, or area where you are grouping these types of orders. One skid or area will have all of the boxes that are just single box orders. Another skid or area will have orders that have two boxes. And another skid or area will be for orders that have three boxes. Keep adding areas for the number of boxes in the order, so you can group them. You might also want to use a rolling bin or box for the small orders that come in Tyvek bags to keep them together.
- As the packages are coming in, check each for any damage. This can be handled quickly with a visual inspection. Have a process in place for what to do if you discover a damaged carton and what is inside is affected.
- Count each package, box, bag, or carton. Does your total match what the freight carrier said was to be delivered? If so, sign for the delivery. However, if the number is off make sure the driver finds what is missing before zooming off. They can be impatient, so this is up to you to enforce and stand firm.
Receiving Department Package Verification Process – Step 1
Now that you have signed for the goods, it is time to find out what is now in the building.
Here is a step by step method that can give you an efficient edge on this work:
- Start with any Rush or critical items. Those have to be processed first, and your Receiving team should have been notified about those earlier. The scavenger hunt begins with these.
- Work the smallest quantity to the largest quantity. As usually a single or small quantity of garments in a Tyvek bag is the remainder for an order that is partially received, start with those. Then do the single boxes. Then orders with two boxes. Followed by orders with three boxes, and so forth.
- Your team member should use the packing slip that accompanies each package and compare what is on the slip to what is inside. Everything should match exactly.
- Use the packing slip as the guide only at this point. Confirm that what is on the packing slip is actually the items before you.
- If everything is correct, the person verifying the content should initial the packing slip and date it.
- But if there is a problem, discrepancy, or question, flag it with a post-it note on the packing slip, place the item(s) back in the package, and move it out of the way for follow-up later in the day’s process. Don’t try to solve it right then. Go onto the next package to check in.
- When everything is processed, go back and follow up on the problem items and work through toward resolution.
Receiving Department Package Verification Process – Step 2
By now, everything that has been delivered should have been checked in by a Receiving team member, and the items verified to the packing slip. If not, go back and finish.
The next step involves verifying the checked-in items on the packing slip to what is in your system on what should be needed for the order.
- Again, start with the smallest quantity and work up to the largest. Those packages with one or two items are usually the partials that can make up the final pieces for an order. Get them received first.
- On the packing slip should be the PO#, name of the client, or another way to look up the order in your system. Pull it up, and verify what is on the packing slip is what is needed for the order.
- You are matching for SKU, color, quantity, size, and any other bit of information.
- If everything matches, the order should be marked “Received Complete.”
- But, if something is missing then the order should be marked “Received Partial”.
- Either way, print a box label that has the order number, name of the job, customer name, and quantity information. Place this on the upper left-hand corner of the short side of the box.
- If the order is completely received and ready for production bring this to the Production Staging area. Segregate by the last digit of the Work Order number.
- If the order is partially received, write a large “P” on that box label so everyone knows that the order is not fully received. While you are waiting for the remaining items, the box is staged in the Partially Received area, and segregated by the last digit of the Work Order number.
- When the missing goods arrive for a partially received order, check them in and then add them to the previously checked in inventory. Print out a new box label and cover up the one with the large “P” on it. Move the inventory from your partial area to production staging.
Receiving Department Inventory Staging Process
The next step in the Receiving Department process is all about how you organize your fully or partially received boxes.
The idea is to have anyone in the building be able to quickly locate the inventory for an order. Whether fully or partially received, it should be easy and simple to find.
To do this, organize by these simple rules:
- All boxes have to have an identifying box label.
- Every box label is positioned on the upper left-hand side of the short side of the box neatly.
- This allows you to stack multiple boxes and you can visually scan them quickly.
- Organize by the last digit of the Work Order number on the sticker. Work order number 123456 would be segregated into the “6” row.
- The area can be in rows on the floor, shelves on the wall, or other ways to organize the inventory.
- You will need to create space for your daily amount. On some occasions, you may have an empty space on one number or a large pile in another. It’s ok. In a short amount of time that will resolve itself, believe me.
- Stack up to four boxes high for the same order. Four boxes can be moved by one person with a hand-cart or dolly.
- Five boxes or more go on a skid. At five boxes, this can be moved with one person with a pallet jack or forklift.
Receiving Department Large Order Processing
While smaller orders can be counted in per piece, what happens when you have a significant amount of shirts to run in production? Here are some rules of the road to help:
- For orders under 144 pieces, count every shirt to verify that the quantities, color, & size match the order.
- When the order is over 144, verify the quantity based on the case quantity plus the miscellaneous piece box count.
- For example, for an order that is 758 pieces, the inventory would come in as ten boxes of seventy-two pieces, plus one box of thirty-eight shirts. Each box would be opened and verified for size and color, but only the box with the thirty-eight pieces would be counted individually.
- Checking in this order would follow the same order processing procedure as outlined above. An order this size would be on a skid. Stage accordingly.
Receiving Department Packing Slips
As you process the work, you need to have a way to keep control of the packing slips for the inventory as shipments arrive.
Here’s a method that works:
- As you process the items in Receiving, each packing slip is reviewed with the information on it and compared to the information in your system.
- Use a simple bin on the desk to collect them for the day. These will stack up. Keep them as neat as you can.
- At the end of the day, collect them and place them in a normal manilla folder with the day’s date listed on the top tab.
- Each day of the month is then placed in either an accordion file or banker’s box for the month, in daily order.
- Keep these handy for a few weeks as production is working jobs.
- After two months, file these for easy retrieval in a safe location.
- If you need to review a packing slip, now you can access it easily by going to the accordion file or banker’s box for the month, scrolling through to the day, pulling out the folder, and leafing through until you can find the right packing slip.
Receiving Department Errors
Everyone makes mistakes. Me. You. Everyone.
The important thing is that we learn from them and make things better.
One thing that I highly suggest is to keep a list of errors or challenges for each department in your business. A simple spreadsheet will do.
Make a master key, and as problems surface give them an error code. REC1 will be your first one, whatever that turns out to be. Here are some items for you to list as column headers:
- The error date the problem occurred.
- What Work Order number was the problem associated with if any.
- The customer’s name.
- The job name.
- What happened. In a few words describe the situation.
- Who was responsible?
- Record the final total cost to resolve the challenge. Include labor and freight in, if possible.
- List ideas on resolving the problem so it doesn’t happen again.
Keep this up to date.
The Receiving Department management team is responsible for helping create an environment where errors are minimal. This happens with accountability, training, and leadership.
“If you can’t describe what you are doing as a process, you don’t know what you are doing.” – W. Edwards Deming
“A bad system will beat a good person every time.” – W. Edwards Deming
“Quality is everyone’s responsibility.” – W. Edwards Deming
Help Support This Blog
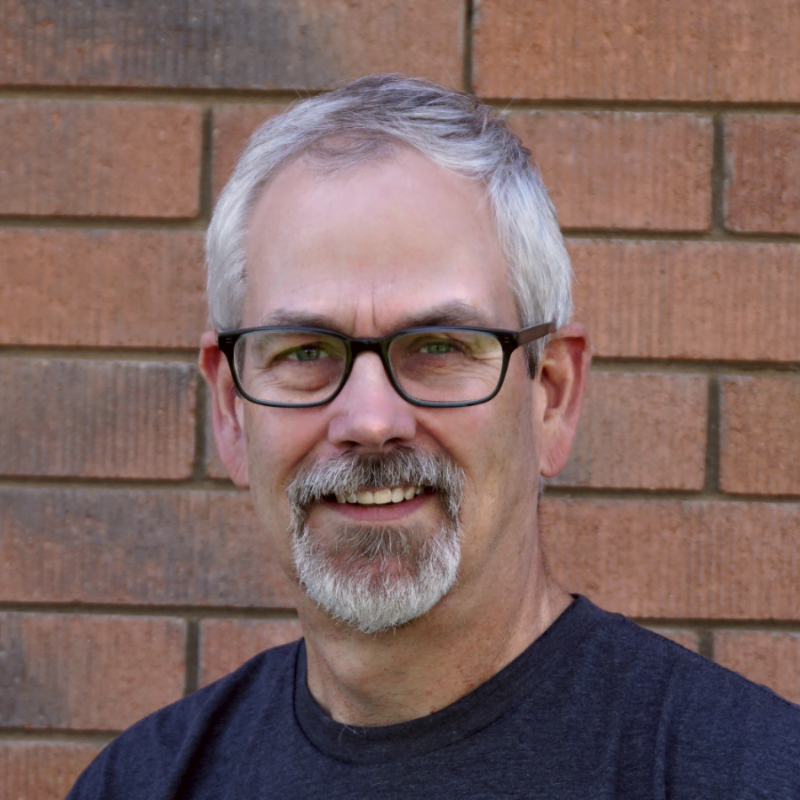
If you like this blog and would like to support it, you can:
- Buy a book.
- Share this blog on your social media.
- Join Shirt Lab Tribe.
- Subscribe to the Success Stories podcast.
- Watch and like an episode on the Jerzees Adventures in Apparel Decorating YouTube series.
- Get signed up for the new Production Tracker app.
Thanks!
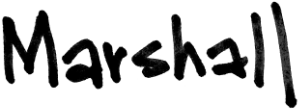